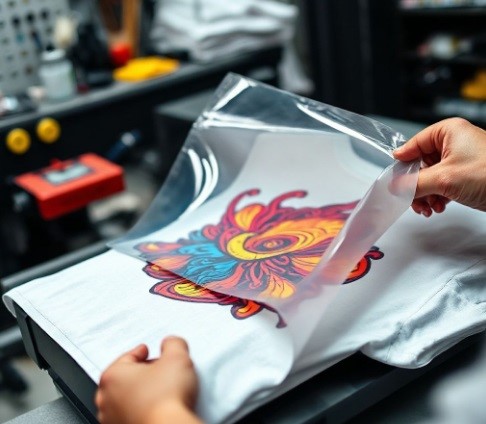
DTF Printing Materials: What You Need to Know
Ever had a client unwrap their custom-printed apparel and exclaim, “This is exactly what I wanted!”? That moment is pure magic. But behind the scenes, that magic depends on more than just great designs or high-tech printers—it hinges on the right materials. Without the perfect transfer film, adhesive powder, and ink, the dream of vibrant, durable prints can crumble into a faded, peeling nightmare.
Let’s uncover the science, strategy, and subtle art of choosing the best direct to film printing materials. Whether you’re a seasoned professional or just starting to explore DTF printing, this guide will transform how you think about the materials at the heart of your craft.
The Science Behind DTF Printing Materials
Printing isn’t just a mechanical process; it’s chemistry in action. Understanding what makes each material tick can elevate your results from average to outstanding.
1. Transfer Films: The Unsung Heroes of Sharp Transfers
Transfer films aren’t just sheets of plastic—they’re engineered marvels designed to carry intricate designs and release them flawlessly onto fabric.
- Hot Peel Films: Think of them as the sprinters of transfer films—quick to act, fast to finish. Made from polyethylene terephthalate (PET) with a release coating, these films allow immediate peeling. Perfect for high-speed operations, but they demand precision to avoid smudging during the peel.
- Why It Works: The release layer is treated with additives that soften just enough under heat, ensuring designs lift cleanly without residue.
- Cold Peel Films: These are the marathon runners—steady and meticulous. Also PET-based, they cool completely before peeling, allowing time for the design to bond deeply with the fabric. The result? Crisp, detailed prints that last.
- A Unique Touch: Cold peel films often include stabilizers that enhance durability, ensuring your prints endure wash after wash.
2. Adhesive Powders: The Invisible Glue Holding It Together
Imagine baking without eggs or glue without stickiness. That’s what direct to film printing would be without adhesive powders. But not all powders are created equal.
- Coarse Powders: Chunky, robust, and ideal for heavy fabrics like canvas or denim. These thermoplastic polyurethane (TPU) granules form strong bonds but can leave a slightly textured feel. Think workwear or tote bags—durable and rugged.
- Fine Powders: Sleek and sophisticated, fine powders are all about finesse. Typically derived from high-density TPU, they melt into delicate fabrics like satin, creating a soft, unnoticeable bond.
- The Science: The particle size impacts the melting temperature and flow characteristics, making fine powders perfect for lightweight, smooth surfaces.
3. DTF Inks: The Alchemists of Color
Inks are where the magic truly happens—where science meets art. The pigments and binders in DTF inks determine vibrancy, longevity, and adaptability.
- Pigments:
- Vibrant reds? Thank azo compounds. Deep blues? That’s phthalocyanine doing its job.
- Tested Standards: Premium inks meet lightfastness criteria (ISO 105-B02) and maintain vibrancy through rigorous wash cycles (ISO 6330). Expect top-tier inks to retain over 90% vibrancy after 20 washes—but verify with independent testing.
- Binders:
- Think of binders as the glue that holds it all together. Water-based polyurethane dispersions ensure flexibility, preventing cracks even on stretchy fabrics.
Choosing the Right DTF Materials: Precision Meets Practicality
Every choice you make, from powders to films, impacts the final product. Here’s how to make decisions with confidence.
1. Durability Matters
- Look for materials certified under ISO 6330 for laundering durability.
- Pro tip: Conduct your own tests. Wash a sample 20 times at 60°C and compare it to the original. Does it retain at least 90% vibrancy? If not, it’s time to rethink your choice.
2. Prioritize Color Accuracy
- Evaluate inks based on their CIELAB color gamut. Aim for ΔE < 3 to ensure true-to-life colors that match your client’s vision.
- Example: Brands like Image Armor are renowned for wide-gamut CMYK+White ink sets, delivering stunning results even on dark fabrics.
3. Match Materials to the Job
- Heavy fabrics like denim? Go with coarse powders and hot peel films for rugged durability.
- Lightweight materials like silk? Pair fine powders with cold peel films to achieve seamless, soft finishes.
When Things Go Wrong: Troubleshooting DTF Challenges
Even the best setups can run into hiccups. Here’s how to fix common issues.
1. Inconsistent Adhesion
You press, peel, and—disaster strikes. The print doesn’t stick. Why?
- Potential Causes:
- Uneven heat distribution.
- Residual moisture in the fabric.
- Solutions:
- Always pre-press the garment for 5 seconds at 160°C to remove moisture.
- Ensure even pressure across the platen. Use a heat gun to verify uniform temperatures.
2. Poor Print Quality
Nothing breaks your heart faster than seeing banding or blurry designs.
- Defects and Fixes:
- Banding: Likely caused by clogged nozzles or inconsistent ink flow. Regularly clean your printheads and use high-quality inks.
- Mottling: Uneven powder application is the culprit. Switch to an automated powder applicator for consistency.
- Color Bleeding: Upgrade to films with consistent coatings to prevent ink migration.
DTF vs. Other Printing Technologies
Here’s where DTF shines—and where it faces competition.
1. Cost Comparison
- DTF: Entry-level printers range from $2,000 to $5,000, making them accessible for small businesses.
- DTG: High-end models start around $10,000, but their direct application excels on cotton-based fabrics.
- Screen Printing: Economical for bulk production but prohibitive for small runs due to setup costs.
2. Production Volume
- DTF: Perfect for short-to-medium runs with quick turnarounds.
- Screen Printing: Best for massive, repetitive orders where economies of scale matter.
3. Design Complexity
- DTF wins with intricate, multicolor designs, handling gradients and fine details effortlessly.
- Screen printing struggles with fine details, especially when layering colors.
Best Practices for DTF Printing
Success isn’t just about materials; it’s about how you use them.
1. Store Smart
- Follow manufacturer recommendations: 15°C–25°C and 40%–60% relative humidity. Airtight containers prevent powder clumping and film warping.
2. Master the Heat Press
- For heavy fabrics: 165°C, medium pressure, 20 seconds.
- For delicate fabrics: 150°C, light pressure, 15 seconds.
- Tip: Regularly calibrate your press to avoid uneven pressure or inaccurate temperatures.
3. Quality Control Is Key
- Perform wash tests under ISO 6330 standards.
- Inspect under controlled lighting to catch defects invisible to the naked eye.
Conclusion: Create Prints That Wow
Picture this: Your latest design is pressed onto a shirt. The colors pop, the lines are razor-sharp, and your client is grinning from ear to ear. That’s the power of mastering direct to film printing materials.
By understanding the science, choosing the right components, and fine-tuning your process, you can deliver prints that leave a lasting impression—every single time. Whether you’re expanding your direct to film printing service or perfecting your craft, now’s the time to aim for greatness. Start today.